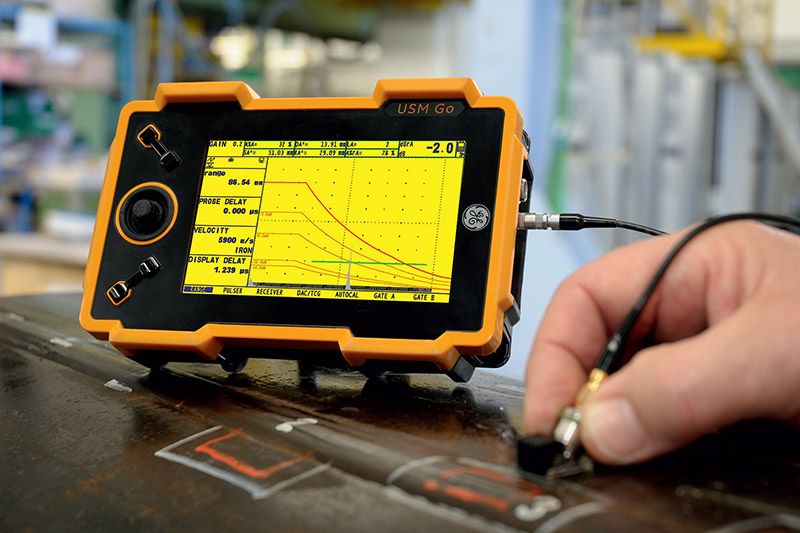
Ultrasonic testing is an NDT technology for detecting test piece discontinuities which may not be visible to the human eye. These defects can include cracks, corrosion, inclusions, porosity outside of specified tolerances, and voids. Ultrasonic testing devices pass ultrasonic sound waves into the test piece and measure the waves that reflect back to the device. The profile of the reflection is interpreted by software and the human operator to determine if the test piece is within spec.
In this article, we’ve interviewed several experts on ultrasonic testing. We hope to provide an overview of this technology and the good which it is doing in the world. We asked our panel of experts the following questions:
- How is ultrasonic testing creating a safer world?
- What advice do you have for someone who wants to start a career in ultrasonic testing?
- What is the most serious flaw you’ve ever detected via ultrasonic testing?
You can jump straight to an expert’s answer by clicking the links below.
I. Stephen Berg | President | Berg Engineering and Sales Company, Inc.
II. Mike Giannini | Business Development Manager | Magnaflux
III. Ian Moore | Advanced NDE | Acuren
IV. Michael Wright | NDT Research Scientist – Group Leader | Eclipse Scientific
V. David Bongiovanni | President & Founder, NDT.org | Founder, Workpad.com
VI. Nick Ferguson | Level 3 | NDTCalc.com
VII. Joseph J. Meyers | Corporate Quality NDE Technical Leader | Scot Forge Company
VIII. Rick Lopez | Deere & Company
IX. Lonnie Anderson | Quality Assurance Specialist | Fish & Associates, Inc.
X. Peter Brunnengraeber | Senior Engineer | aycan Data Management
I. Stephen Berg | President | Berg Engineering and Sales Company, Inc.
Stephen Berg entered the nondestructive testing industry in 1996. He began in the world of ultrasonics, then added expertise in eddy current testing, magnetic particle, penetrant, thermal imaging, and remote visual inspection. He was involved at the beginning of automation and hardness testing and image analysis. At Berg Engineering, he built a service organization from the ground up and has led his team to 10+ years of ISO accreditation. Berg Engineering was the first company to achieve the ISO 17025 certification for nondestructive testing.
1. How is ultrasonic testing creating a safer world?
Ultrasonic testing is creating a safer world by verifying the integrity of processes and manufactured products. It is used to monitor corrosion where it cannot be seen by the human eye. It is used to check the integrity of welds in petrochemical, power, and automotive industries. It is used to check for issues with castings and forgings. It has a critical role in checking components of aircraft without damaging the components. It is used to check new materials and composites for integrity. In all these cases, the product is not harmed by testing.
2. What advice do you have for someone who wants to start a career in ultrasonic testing?
One thing I would say is to go through a good certification process. Choose a job that has different applications to work with. Always continue with education and certifications. Work with integrity—that’s the most important thing. Your integrity is your most valuable asset as an inspector.
Keep up with current standards and specifications, if applicable, and become a member of the local ASNT chapter. Keep up with ASTM standards. There are at least 500 ASTM standards for ultrasonics. It’s never ending.
Last but not least: never stop learning.
3. What is the most serious flaw you’ve ever detected via ultrasonic testing?
We found a small inclusion in a bar that was being used for a critical safety-related part in the automotive industry. This defect would have caused the braking system of the car to fail. They already had one failure because of it, and we were able to find the issue in the bars. Some of the stock was bad, but not all. There’s no telling how much damage would have been done if this problem was not detected.
II. Mike Giannini | Business Development Manager | Magnaflux
Mike joined Magnaflux in 1973, after receiving a BS in Metallurgical Engineering from Michigan Tech. He left Magnaflux after five years to work in the Inspection Department at Republic Steel, writing and presenting personnel qualification programs for inspection personnel. He operated an independent sales rep organization for twenty-five years before returning to Magnaflux. In the last eleven years he has concentrated on developing custom inspection solutions for Magnaflux customers, including high speed resonant inspection systems. His career includes more than forty years in Quality and Inspection.
1. How is ultrasonic testing creating a safer world?
Ultrasonic testing is used every day in a variety of infrastructure inspections that the public passes, but doesn’t see. Bridges and highway signs are inspected periodically for corrosion, weld integrity, and the soundness of the fasteners that support light pole and highway signs. It is used to inspect construction equipment during manufacturing, and it is used to inspect pipelines as sections of pipe are joined, and before those sections are buried.
2. What advice do you have for someone who wants to start a career in ultrasonic testing?
Start by getting training at a quality facility that is recognized by the industry. Today’s flaw detectors take the math out of setups and evaluation, but it’s a good idea to go through the math by hand to gain a thorough understanding of the technique. Trigonometry can be painful, but understanding how sound travels in materials is critical to good inspection.
3. What is the most serious flaw you’ve ever detected via ultrasonic testing?
Early in my career, I visited a hangar in Texas that was filled with main rotor blades from a model of light observation military helicopters. The Army and Navy both used versions of this aircraft and had discovered a flaw in the welded structure that formed the core of the rotor blades. The entire fleet was grounded pending ultrasonic inspection, but the two services couldn’t agree on how to apply the technique that one of the services had written.
III. Ian Moore | Advanced NDE | Acuren
Ian has 25 years in the NDE business with Acuren as an NDE technician, Advanced NDE Technician, Supervisor, and Office Manager. He has worked with and has knowledge in UT, MT, PT, RT, AUT, Phased Array, IRIS and API 653 Tanks inspections.
1. How is ultrasonic testing creating a safer world?
UT has given us the ability to test the integrity of items that was not possible prior to the invention of some of these technologies. It has also reduced the risk of running them at high pressures and increased the safety of the people that work around them.
2. What advice do you have for someone who wants to start a career in ultrasonic testing?
Acquire as much experience in UT as possible before becoming a level 2, and get a good understanding of the material metallurgy. This will help you understand the failure mechanisms that you will be looking for with UT. In some cases, UT is not your best method of inspection.
3. What is the most serious flaw you’ve ever detected via ultrasonic testing?
I was inspecting a large nozzle (1.5” thick) coming off a vessel (2” thick) during a shutdown that while is service contained Hydrogen at an elevated temperature. While inspecting the weld I detected that the weld was cracked approximately 6” long and 0.750” deep. This could have caused a significant explosion if it failed while in service. The cost to repair was high but the cost of a failure was immeasurable. The client was both grateful it was found and upset that they had not planned for the repair.
IV. Michael Wright | NDT Research Scientist – Group Leader | Eclipse Scientific
Michael Wright leads Eclipse Scientific in NDT research. He is the author of several acclaimed NDT textbooks.
1. How is ultrasonic testing creating a safer world?
Before UT testing, there was visual testing and a few surface testing methods, but subsurface inspection was not available. Being able to test a component for subsurface indications helps to ensure that a component has no indications that can cause failure of the part.
Ultrasonic Testing (UT) is a nondestructive testing method, so it can be applied directly on a part or component that will actually be used for its purpose. This means it can be used for each and every part instead of destructively testing a small sample of parts and inferring that destructive results represent all the parts. This type of testing is far more accurate than statistical sampling. Also, UT can be used on parts currently in use for inspection of in-service defects.
UT is used extensively in aerospace to ensure aircraft are safe for flying.
The nuclear industry uses UT for hundreds of components to ensure they are safe for service and for preventative maintenance.
The pipeline industry uses UT for weld safety as well as preventative maintenance.
Structural steel welds, from building frames to bridges, are inspected to ensure there are no defects that can cause structural failure over time.
Industrial facilities use UT for new fabrications and for preventative maintenance. Preventative maintenance helps to avoid industrial accidents that can not only cost money, but can also cost lives.
The rail industry inspects all rail for structural integrity to ensure the rail is safe for a train to travel over.
The medical industry uses UT for medical diagnosis. Understanding what a patient has can save their life.
2. What advice do you have for someone who wants to start a career in ultrasonic testing?
I have the following 3 pieces of advice:
- Have patience and learn everything you can whenever you have an opportunity to learn. A person needs patience as the entire certification process is long and has many steps. The theory is also something that is progressively learned. A person cannot simply start with the most advanced techniques and expect to do very well. It takes patience with the practice to stick with it until someone becomes proficient.
- Practice, and practice some more. Conventional UT is not extremely complex, but it takes a feel that cannot be learned with theory alone. The more practice a person has with a probe in their hand, the better they will become at learning the feel. With practice, a UT signal can be made more repeatable. The more practice a person has with UT signal interpretation, the easier it becomes. Understanding the significance of one signal over another is only learned through practice.
- Read procedures and code early in your learning. Procedures take practice to understand and to be able to create. The more experience you have with them the easier and more natural making them becomes. Code is rather cryptic until you have been exposed to lots of it. Once you get used to the language and purpose of the sections, code becomes understandable and it is easier to learn what you require from it.
3. What is the most serious flaw you’ve ever detected via ultrasonic testing?
I was part of a team of inspectors at a reactor during a shutdown. We detected a thin spot on the lower vessel that was nearly half a square meter. This region was so complex to repair that it took more than 4 months and over 1000 people to achieve its successful repair.
V. David Bongiovanni | President & Founder, NDT.org | Founder, Workpad.com
Mr. Bongiovanni has over 20 years of experience designing hardware and software for the inspection industry. His roles have included research and design engineering for Visual Inspection Technologies, Inc., now a part of GE Digital; founding NDT.org, the largest global network of quality and inspection engineers; and founding Workpad.com, the cloud solution for managing and reporting inspection data.
1. How is ultrasonic testing creating a safer world?
Ultrasonic testing is the primary method of detecting flaws in any mission-critical component in aerospace, infrastructure, oil and gas, and power generation. From LPG tanks to refinery pipes, ultrasonic testing ensures the safety of workers, passengers, and the environment. Corrosion never rests, and ultrasonic testing is our first line of defense to ensure failures are minimized with efficient and complete monitoring and maintenance.
2. What advice do you have for someone who wants to start a career in ultrasonic testing?
The two best ways to get into the Ultrasonic Testing discipline of nondestructive testing are apprenticeships and schools. Many companies hire entry level UT techs and offer on-the-job training to allow employees to progress through ASNT Level 1, 2, and 3 certifications. All it takes is a good comprehension of basic math and the willingness to learn.
The school route can jump start one’s UT testing career in as little as six months. NDT.org has a full section dedicated to listing NDT specific programs around the world, including junior and 4-year colleges, online classroom training, and trade unions like the International Union of Operating Engineers Local 112.
3. What is the most serious flaw you’ve ever detected via ultrasonic testing?
Any flaw that can harm a person or the environment is a serious flaw. As an NDT technician, I was lucky enough to work with some of the best operating engineers at fossil and nuclear power plants on the east coast and am proud to say that the vast majority of indications were consistent with the service life of the items we were inspecting and simply validated the maintenance schedule that was already set. That said, defects are found in airframes, boiler pipes, and storage tanks every day, allowing remediation before the problem becomes serious.
VI. Nick Ferguson | Level 3 | NDTCalc.com
1. How is ultrasonic testing creating a safer world?
Ultrasonic testing and all other nondestructive methods have helped create a safer world by allowing engineers, asset owners, and organizations to gauge the integrity of their assets. Non-destructive testing, as a small example, is used to determine whether aircraft are safe to fly, if bridges are safe for vehicles to drive over, if nuclear power stations are safe to keep running, and if newly fabricated constructions are fit for use. Nondestructive testing allows the inspection of all of these items, plus many more, without interrupting their day to day use. Without nondestructive testing, there would be no way to determine the fitness for purpose of an asset without physically pulling it to pieces!
2. What advice do you have for someone who wants to start a career in ultrasonic testing?
To get into a career in ultrasonic testing and all other methods of NDT, there are a few requirements. First, it’s strongly recommended that candidates hold a qualification or relevant experience in manufacturing or heavy engineering—i.e., that they have an understanding of the components they’re testing, how to read drawings, and understand the welding or fabrication techniques used to manufacture the items they’re inspecting. Persons wanting to get a career in NDT have to sit an approved course (offered by many training bodies around the world), then gain a nominal number of hours (hundreds of hours!) of experience before then applying for ISO 9712 certification to become a certified technician. The main certifying bodies are the Australian Institute for Nondestructive Testing, the British Society for Nondestructive Testing, and the American Society for Nondestructive Testing.
Once certified, technicians will then be approved and certified to conduct NDT inspections against industry standards to approve inspected items as fit for use. A career in NDT could get you working in the oil and gas industry, the mining industry, offshore, on aircraft, or on vessels being sent to outer space!
3. What is the most serious flaw you’ve ever detected via ultrasonic testing?
Every defect is serious. As an example, the smallest (less than 2mm) defect in a railway axle could eventually grow to snap the axle if not detected. Then again, some mining equipment, such as excavators, allow for defects over a foot long. The severity of the flaw depends on the item that’s being inspected. NDT can be used to gauge the health of pieces of non-critical equipment or can be used to inspect for defects, that if not found, can cause catastrophic and life threatening failure.
VII. Joseph J. Meyers | Corporate Quality NDE Technical Leader | Scot Forge Company
1. How is ultrasonic testing creating a safer world?
Ultrasonic testing ensures the suitability of a product before its use, or a level of assurance for its continued use. Ultrasonic testing is largely used for detection of internal discontinuities that are not visible to the naked eye. While some techniques within ultrasonics can be used to detect surface discontinuities, an additional trigger is needed to draw attention to these potential defects. Ultrasonics provides this.
Placing a product with a defect into service can be catastrophic. Not only will the structure fail, but loss of life can ensue. While we cannot place a number on just how many lives are saved through all the practices of ultrasonic testing per year, if just one life, crew, or mission is saved, the industry has done its job.
2. What advice do you have for someone who wants to start a career in ultrasonic testing?
The best advice I can give is to sit in the passenger seat for as long as you can and observe and work with as many technicians as possible. Throughout my 13 year career, I have worked with a number of certified technicians, and this learning process has never ceased. Many of your industry technicians may perform the same task or work to the same procedures, but all have each had their own understanding and personal preferences of how to perform their needed tasks.
While working with these diverse teams and absorbing certain tactics and knowledge, this can mold you into an incredibly effective technician. With developing this true understanding you are not just another technician performing important inspections, but rather a valuable tool for the industry to help make the world a safer place.
3. What is the most serious flaw you’ve ever detected via ultrasonic testing?
The most serious flaws I have encountered have been those that are at the threshold of acceptance. The specifications and procedures will dictate when a flaw is acceptable or rejected. There are times throughout your career when you will encounter a flaw or discontinuity that is at that threshold. This is where the real talent and competency of a technician comes into play. Interpretation and execution of the examination is key. For contact ultrasonics, this can mean probe selection, scanning pressure, probe position, couplant adequacy, surface finish consistency, and any needed compensations, to name a few. Anything less than executing at 100% compliance could be devastating for the end use.
VIII. Rick Lopez | Deere & Company
1. How is ultrasonic testing creating a safer world?
Ultrasonic testing is used to monitor manufacturing processes and to evaluate a part’s acceptability against a set of criteria. Even when those parts aren’t used in applications typically thought of as “mission critical” (e.g. aerospace), failure of a key component could lead to injury or worse for direct users of a piece of equipment, or those around them. In the quest for distinctive product quality, example UT applications may seek to detect flaws in welds or wrought products, estimate coating or layer thickness, or monitor casting production for desired microstructure. When components are able to meet all of their design expectations, then safety factors are met.
2. What advice do you have for someone who wants to start a career in ultrasonic testing?
From an engineering perspective ultrasonic testing (UT) knowledge, regardless of job function within the manufacturing industry, is a valuable thing. Even if that person is not proficient enough to be an independent technician, UT exposure may be useful at any stage within a component’s lifecycle. It may be considered at the design stage (i.e. design for inspectability), used during inspection of parts after primary or secondary processing, or used during periodic checks throughout the end product’s lifetime. This means that design, materials, manufacturing, quality, and other types of engineers and managers could all benefit from UT background knowledge. Deep UT knowledge is fairly rare, and as a consequence it can make you a highly sought-after potential employee and a great resource for the company once you are hired.
IX. Lonnie Anderson | Quality Assurance Specialist | Fish & Associates, Inc.
Mr. Anderson is a certified welding inspector (CWI) and Level II NDT specialist with a technical college certificate in welding and an associate’s degree in nondestructive testing. He has a thorough understanding of welding processes for a variety of materials and over twenty years of experience in structural steel welding, fabrication, and inspection. He has supervised welding fabrication of steel, aluminum, and stainless steel elements of equipment and structures. He is a lead inspector for shop fabrication inspection and on-site inspection of steel connections and cold-formed metal stud inspection, performing visual inspections, ultrasonic testing, magnetic particle testing, dye penetrate testing, shear stud inspection, metal deck weld inspections, and bolt tension inspection.
Mr. Anderson also performs reviews and approval of weld procedure qualification records (PQR), weld procedure specifications (WPS), and welder qualifications.
1. How is ultrasonic testing creating a safer world?
Ultrasonic testing (UT) ensures that high quality welds are created in the building and bridge industries.
UT is performed on new and existing welds to detect a defect that is not identifiable on the surface by
visual inspection. Ultrasonic testing ensures a properly welded connection and as a result, a safer
building or bridge.
2. What advice do you have for someone who wants to start a career in ultrasonic testing?
Learn how to weld first. I have a background in welding and it has really helped me advance in the field
of UT. Learning how to weld and learning the different types of welding defects associated with the
various welding processes will help you understand what you are actually seeing on the UT machine.
Knowing that each welding defect will act differently to ultrasound is critical.
3. What is the most serious flaw you’ve ever detected via ultrasonic testing?
Detecting a sizable wear grove on a bridge pin.
A pin and hanger assembly is used to connect two plate girders of a bridge. These assemblies are used
to provide an expansion joint in the bridge. One girder (anchor span) is set on a pier with a short section
cantilevered out toward the next pier. The other girder (suspended span) begins underneath the anchor
span, and has its far end resting on the next pier. The girders have holes directly above each other. The
two holes are connected using hangers and a pair of connecting plates sandwiching the bridge girders. A
pair of large steel pins through the plates and webbing provides the hinges, holding up the suspended
span while allowing it to move longitudinally and rotate. Large nuts with washers are placed on each
end of the pin to retain the hangers. In some cases, the hangers are retained by a large circular plate
that is placed on the ends of the pins that is held in place with a threaded rod that extends through the
pin.
While performing UT on a bridge pin, I observed an indication in the shear plane area of the pin. Further
UT was done on this pin with a couple of different transducers and wedges to verify the indication was
in the shear plane on the bridge pin. It was determined by UT there was a wear groove approximately 4
½” long. The DOT replaced the pin with a new one. The shear plane wear groove was visually verified
once the original pin was removed.
X. Peter Brunnengraeber | Senior Engineer | aycan Data Management
Peter has been designing and implementing data management solutions since 1998 in the manufacturing, e-learning, communications, and medical industries. As Senior Engineer for aycan, Peter leads the US development team in the design and development of standards-based solutions to address customer needs. He is a member of ASNT, ASTM E07 and IEEE, and active in the DICONDE standards group. Peter received his BS in Information Technology from the Rochester Institute of Technology in Rochester NY.
What types of experience will help someone work with digitally stored UT information?
One important but commonly overlooked aspect of digital storage of inspection data is management of that data to ensure recall and integrity when it is needed. Migrating to the use of a indexed archive system allows for an inspection provider to have a simplified, uniform, and audited method for storage of result data. The index allows for quick retrieval by component, inspector, or part name for instance and completely manages the file storage. With typical UT this isn’t quite as large a problem, but with the growth of phased-array UT with their large file sizes and large number of files, management can easily become a laborious task if not automated.